Femoral Insert
Learn how you can produce more femoral implants faster – and achieve longer tool life and better surface finishes.
Watch us machine a femoral, highlighting the shift from cobalt chrome to titanium for better body connectivity and machining efficiency.
To watch the demo, fill in this form now and instantly get 5 additional machining demos
Inline Content - Sugar Form
Sugar Form url - https://info.secotools.com/acton/fs/blocks/showLandingPage/a/45194/p/p-00dc/t/page/fm/0
Frame height - 650 px
Every year, medical implant manufacturers search for new ways to make more parts faster, use fewer tools, cut part costs – and still meet demanding specifications for geometry and surface finish quality.
Today, digital scans can capture every detail of the human knee and additive manufacturing (AM) can create a one-off assembly, including a femoral knee implant. Other manufacturers create femoral implants in higher volume from forgings, castings or solid billets of cobalt chrome or titanium.
Machining the femoral implant calls for specialized tools that can handle its deep box wall structures and the complex geometry of its dual condyles. To make the part in titanium, manufacturers may need to switch from grinding to machining, which increases cycle times.
Seco offers several ranges of ball nose end mills that provide excellent performance on the femoral implant. With a unique geometry and coating, the JH780 can rough and finish the box wall. The JH730 can finish outside profiles. The JH112 and JMB112 offer highly stable performance. The JH722 maximizes stability and strength in 5-axis machining.
Tooling manufacturers offer high-quality tools for their customers' applications and the industry expertise to recommend the right approach to each process. When medical implant manufacturers partner with an experienced supplier, they can raise part quality and optimize their output. As a trusted adviser, the right supplier can guide medical implant manufacturing toward success.
JH780 taper ball nose end mills rough and finish the box wall with a unique geometry and coating. The tool's tip radius can be effective with limited tool positions.
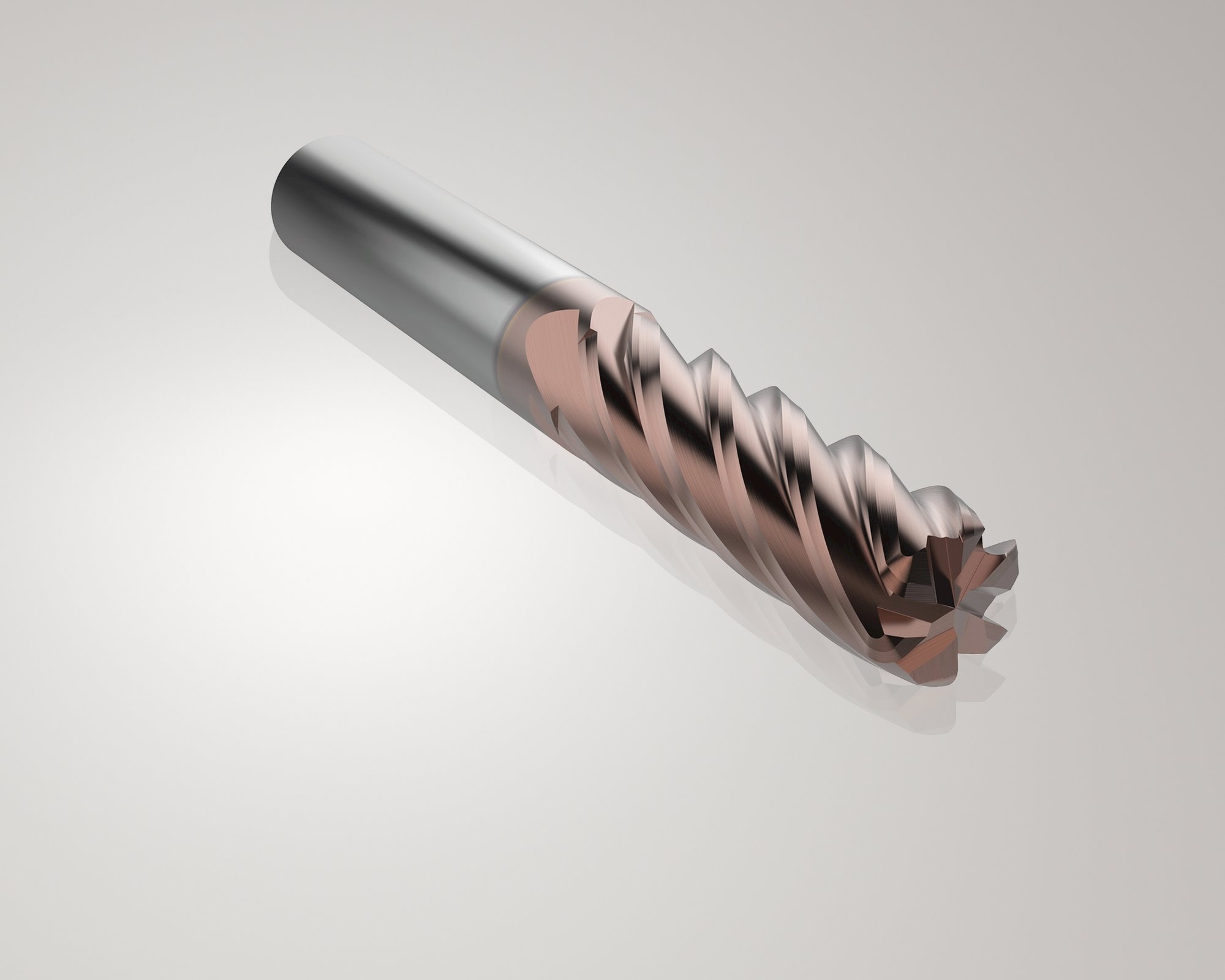
JH730 high-speed end mills cut vibration with differentially spaced flutes and can finish outside profiles.
JH112 high-speed, high-precision ball nose end mills and JMB112 two-flute miniature ball nose cutters offer highly stable performance.
The short flutes of JH722 ball nose end mills maximize stability and strength for condyle surface machining, with long reach for 5-axis articulation.
JH724 and JH726 barrel end mills reduce cycle times, but parts may need belt surface grinding before polishing.
As part specifications increasingly replace cobalt chrome with titanium for production of femoral knee implant for complete knee assemblies, medical device manufacturers need to switch this part from grinding to machining. Grinding creates heat zones that change the properties of titanium. In turn, this affects the viability of the finished part, especially over time and under the weight-bearing stress of the patient's gait. But machining yields longer cycle times than grinding, so manufacturers must look for other ways to raise their production output and meet competitive demand. At the same time, manufacturers must minimize burrs and the need for secondary manual polishing process to remove them.
The human knee is a marvel of natural engineering, and when a complete knee assembly replaces it, the implanted parts must provide equivalent functionality. At the lower end of the femur, the femoral implant must provide smooth performance as the knee bends and straightens under a patient's weight.
Traditional tools struggle to reach the interior of the femoral knee implant, where the box requires superior finishes.
The unique geometry and coating of the JH780 taper ball nose end mill series (typically R1 and R1.5) achieve these finishes easily, producing straight box walls and running within machining tolerances for longer periods of time.
To optimize production, the JH780 series is available with multiple radius and taper angles.
To finish the box wall of the femoral knee implant, manufacturers must reach the constrained interior of the part. The JH730 high-speed end mill series includes either six or seven flutes with differential spacing that reduces vibration. It includes both the right geometry and the ideal polished coating for long tool life. This tool series can be too large to work within the femoral implant box, however, but it can serve as a good choice to finish the outside profiles.
Again, tool size becomes a consideration. For optimized roughing, the JH112 high-speed, high-precision ball nose end mill and the JMB112 two-flute miniature ball nose cutter offer extremely stable performance. Manufacturers also can use the tip radius of the JH780 when machining situations limit tool positions within the machine itself. Although the JH730 high speed end mill series can produce good machining results, most of its diameters exceed the work area.
This application can produce long cycle times, short tool life and excessive breakage.
The JH722 six-flute ball nose end mill series offers short flute lengths for maximal stability and strength. Its long reach accommodates 5-axis articulation over the component surface, and its tightly controlled radius tolerances yield surface finishes that comply with design specifications.
With four and six flutes respectively, the JH724 and JH726 barrel end mill series can reduce machining time dramatically and avoid the need for expensive grinding machines, but the parts they produce can require belt surface grinding before polishing.
Of these two series, the JH724 can provide consistent reliability in this application and the JH726 provides further productivity improvements.
Productivity demands process optimization that increases production speed, enables higher quality and produces the correct conditions for unattended production. With the right tool geometries and performance, manufacturers can optimize production reliability, achieve uninterrupted output and eliminate productivity bottlenecks. For the femoral knee implant, the biggest complication lies in selecting tools that provide the necessary high-speed, high-precision performance in constrained spaces.
Ideally, a tooling supplier becomes a medical implant manufacturer's partner as well as a source of great tools. Additional services enhance the quality of the relationship and its value to the manufacturer, including tool reconditioning for better amortization of costs, consulting expertise that assists in process optimization and a reliable supply of the necessary tools.
A tooling supplier must offer a holistic approach to parameters, machines, fixtures and CAM to help manufacturers optimize their entire process and gain maximum value.
Contact our experts here