Choosing the right High Feed Milling Cutter
Discover the best high feed milling cutter for your needs. Browse through our comprehensive range to learn more.High feed milling is a machining method that combines a shallow depth of cut with a high feed per tooth. This approach allows for faster material removal rates compared to conventional milling methods. The cutting forces are directed axially towards the machine spindle, enhancing stability and reducing vibrations, which in turn extends tool life.
When you're picking out a high feed milling cutter, it's important to think about what material you'll be working with and the design of the cutter. Make sure your machine can handle the cutter's demands and keep an eye on the feed rate and cutting speed to get the best results and a smooth finish. Choosing the right cutter and setting it up properly can really boost your productivity and save you money in the long run.
Keep reading to discover Seco’s wide range of high feed cutters.
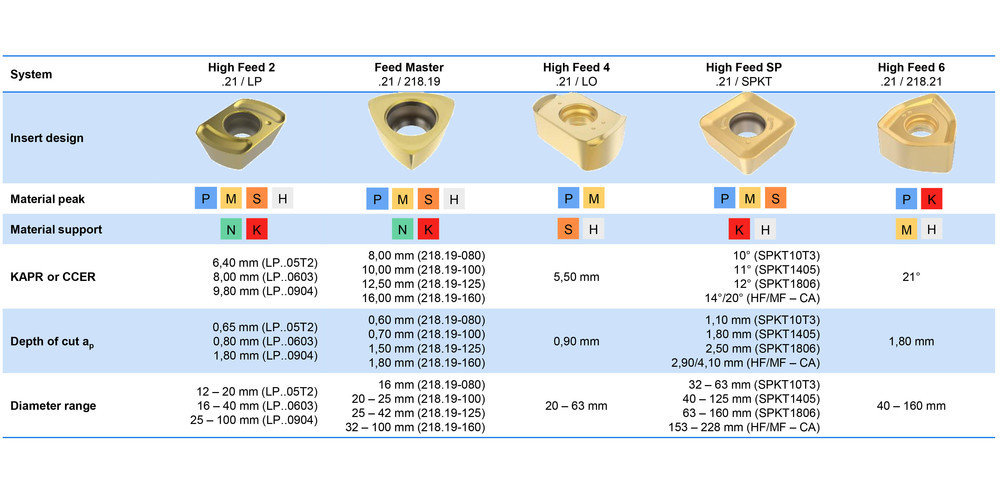
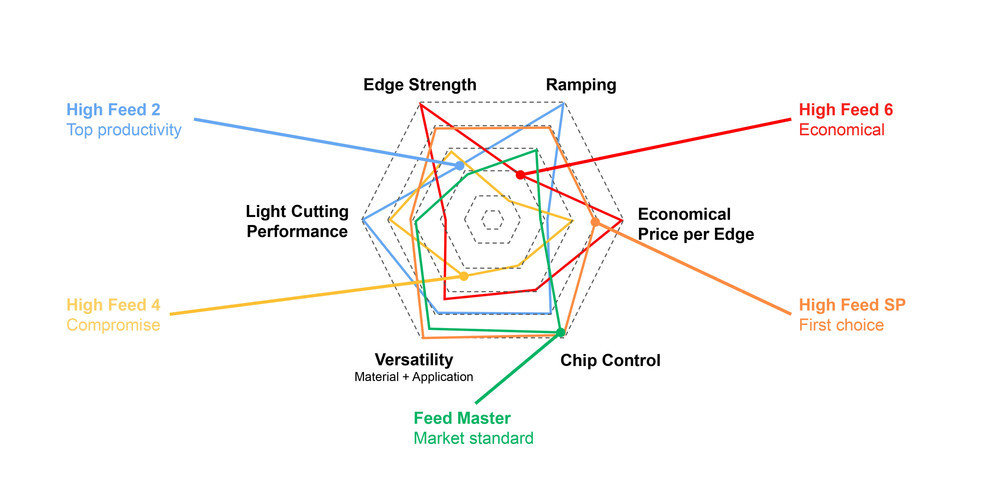
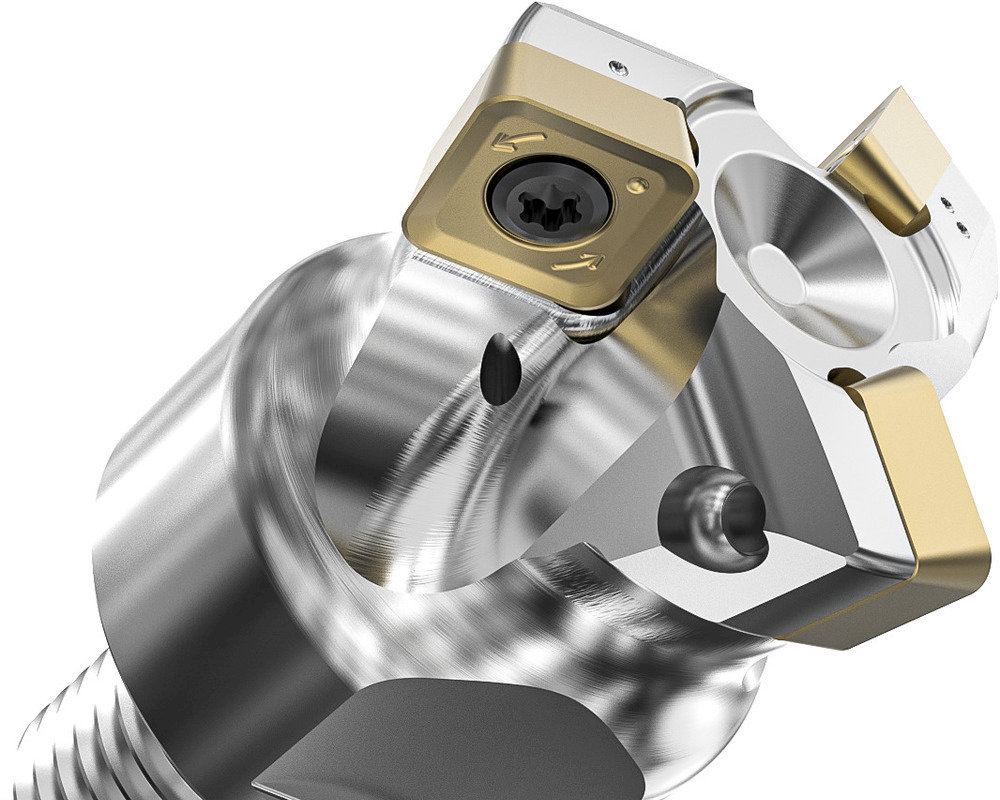
High Feed SP milling cutters are Seco’s first choice for High Feed machining.
With four cutting edges and single-sided inserts they are designed to handle challenging materials efficiently.
They offer superior tool life and lower costs per edge, removing more material faster than conventional milling.
Optimized for steels, stainless steels and superalloys, these cutters ensure high productivity and performance, making your machining operations faster and more reliable.
Key benefits and features:
- Superior Tool Life: High Feed SP cutters are purpose-built to tackle difficult-to-machine materials like stainless steels, titanium, and superalloys. Their design minimizes notched and built-up edges on inserts, extending tool life and reducing breakage.
- Cost Efficiency: The four-sided solution allows for more material removal and makes your tooling budget go further. The environmentally friendly coating on the cutter body also contributes to longer tool life.
- High Productivity: With a fine-tuned approach to cutting, High Feed SP cutters excel in everything from free-cutting austenitic stainless steels to cobalt and nickel-based superalloys. They achieve high per-tooth feed rates across their full depth of cut range, easily controlling chip formation to ensure fast and reliable processes.
- Versatile Applications: Available in three sizes with a complete range of proven geometries and grades, these cutters are ideal for face milling, copy milling, ramping, pocketing, and plunging. Their positive, single-sided square approach ensures a constant lead angle up to the maximum depth of cut.
Go to the products
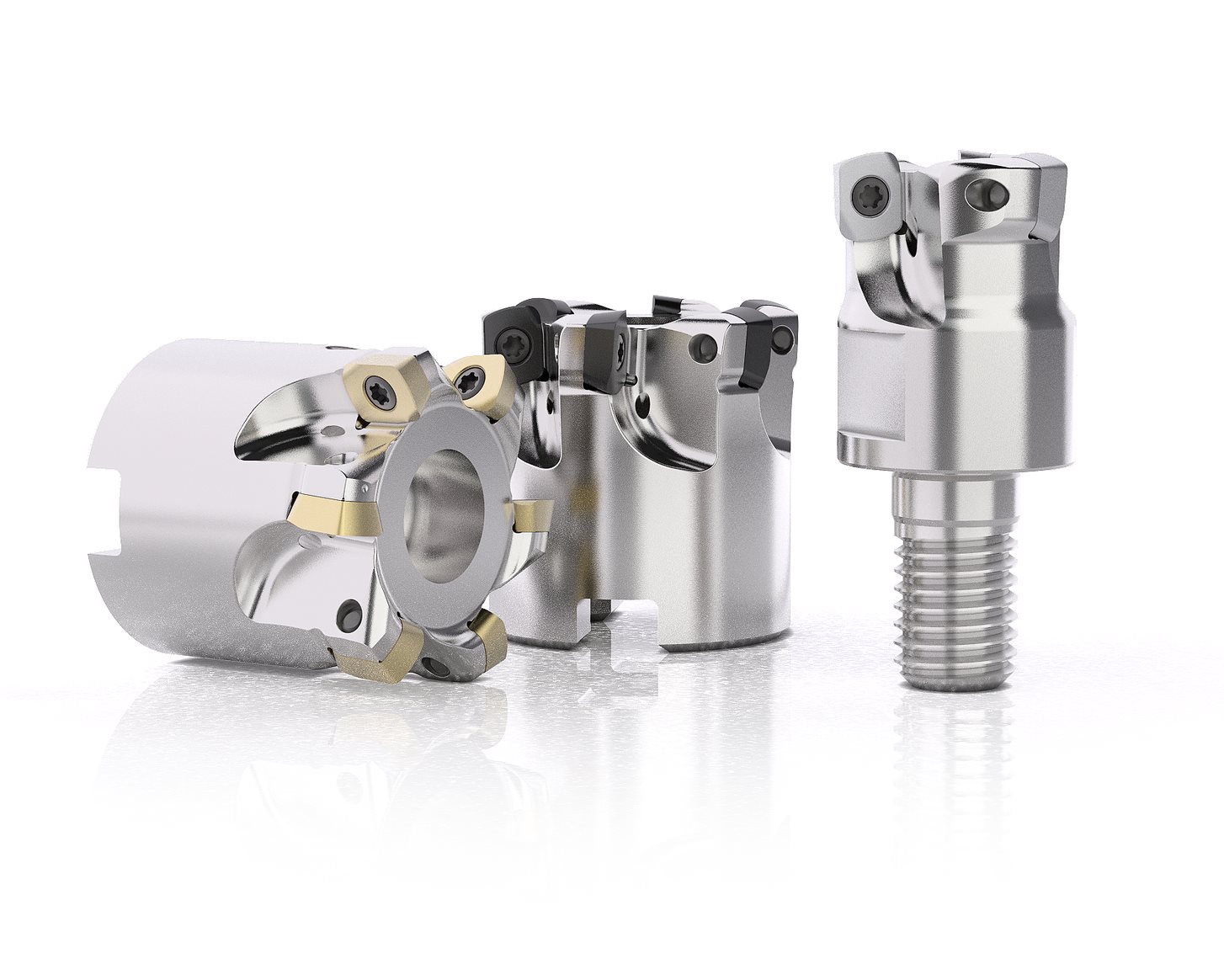
Great for roughing and semi-finishing jobs, High Feed 2 comes in Ø12mm to Ø100mm and are available in Arbor, Combimaster and cylindrical shank styles.
These tools are designed to deliver very high material removal rates, while increasing stability, especially when working with long overhangs.
The inserts have two cutting edges and come in different geometries and coatings, making them perfect for a variety of materials, including hardened steel.
Key Benefits and features:
- Enhanced Stability: The high-feed strategy directs cutting forces axially, which reduces the risk of vibrations, especially in long overhangs while high effective diameter to cutting diameter ratio increases stability.
- Versatility: These tools are suitable for various materials, including superalloys, steel and hardened steel materials, making them a versatile choice for different applications.
- Efficiency: They are optimized for both roughing and semi finishing operations, allowing for near-final shape profile machining.
- Reliability: The inserts have a strong and reliable design with modern geometries, ensuring consistent performance.
- Productivity: Close pitch versions and optimized flutes enhance productivity by allowing for higher feed rates and better material removal rates.
Go to the products
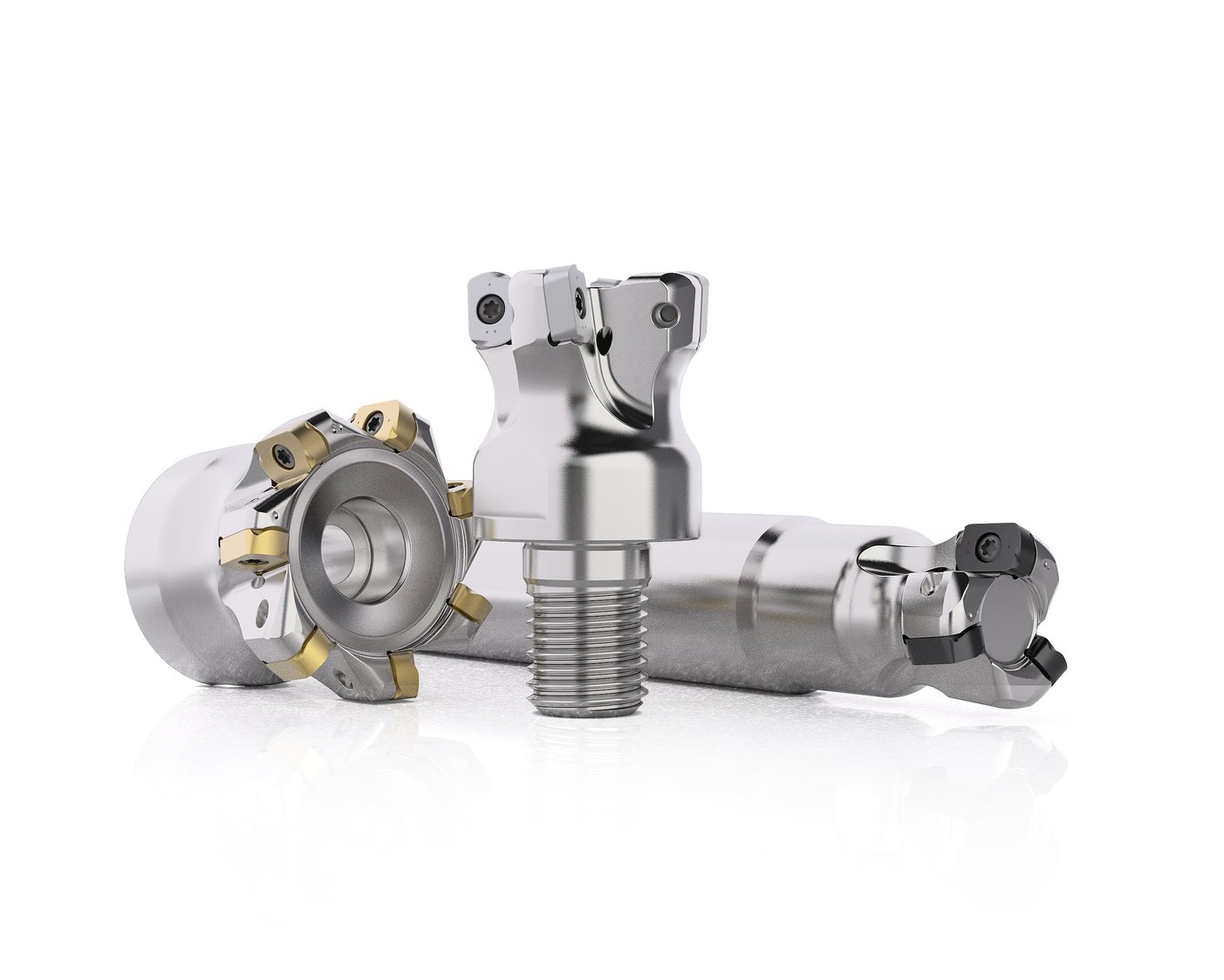
Designed to maximize material removal rates and reduce machining time, especially in challenging conditions such as long tool overhangs, unstable environments, and machining stainless or hardened materials.
The High Feed 4 features a double-sided high feed insert, offering improved productivity, reliability, and economy compared to other alternatives.
Key Benefits and Features:
- Double-sided insert: Provides four cutting edges, enhancing productivity and cost-effectiveness.
- Modern geometries: Ensures smooth cutting and balanced combination of high productivity and good economy.
- Reinforced core: Offers reliable machining and reduces the risk of cutter body damage.
- Optimized flutes: Ensures excellent chip evacuation, enhancing overall machining efficiency.
Go to the products
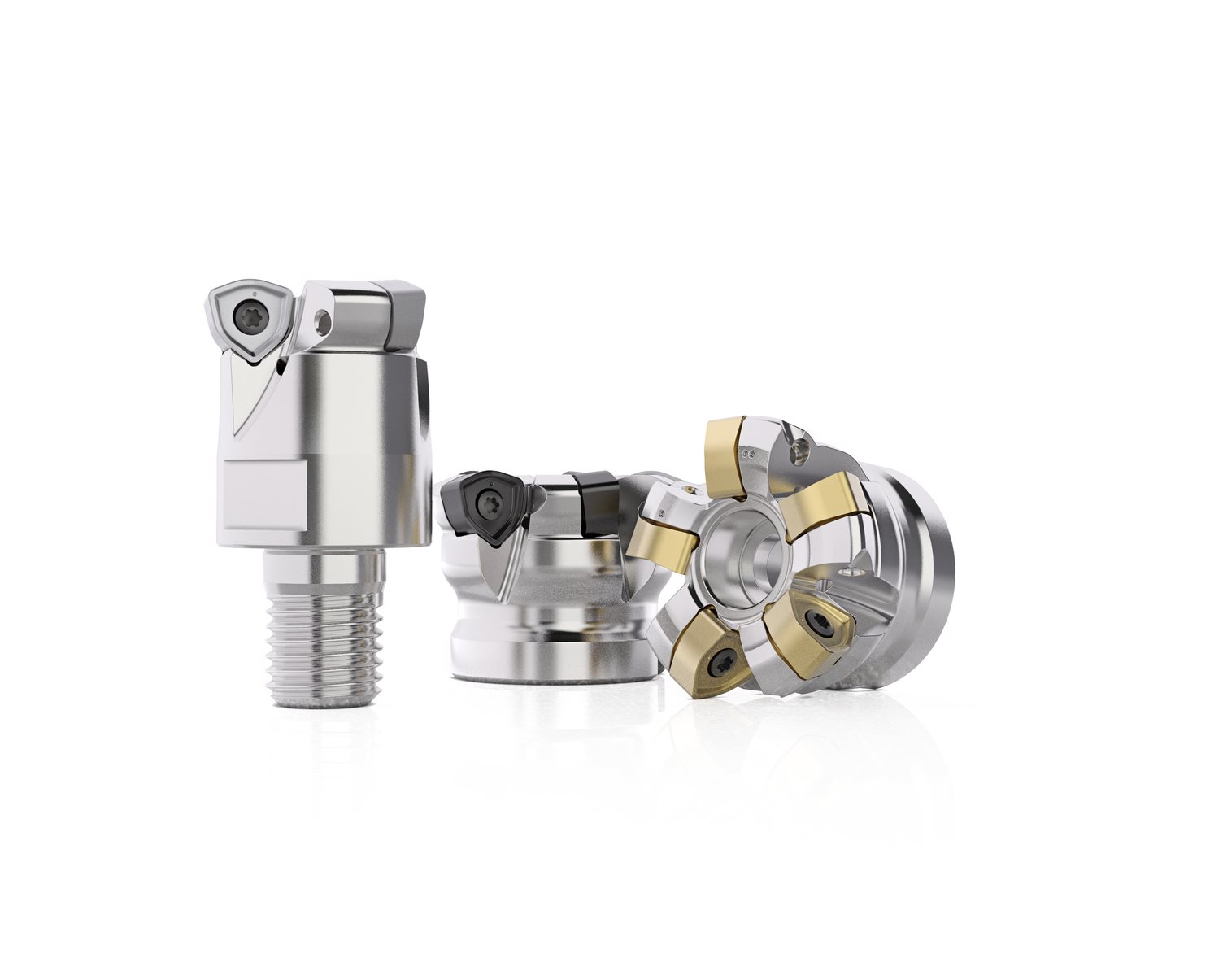
Designed to deliver exceptional material removal rates and low operating costs, the High Feed 6 is ideal for high feed applications, including face milling and plunging.
It is mainly suitable for steel and cast iron materials and features a double-sided insert with 6 cutting edges, ensuring precise and stable mounting, reduced vibration, and long, predictable performance.
Key Benefits and Features:
- Double-sided insert with 6 cutting edges: Enhances productivity and cost-effectiveness.
- Highly productive: Axial depth of cut up to 1.8 mm: Allows for exceptional material removal.
- Versatile applications: Suitable for high feed milling and plunging operations.
- Robust design: Thick inserts and sturdy cutter bodies are ideal for heavy roughing environments.
Go to the products
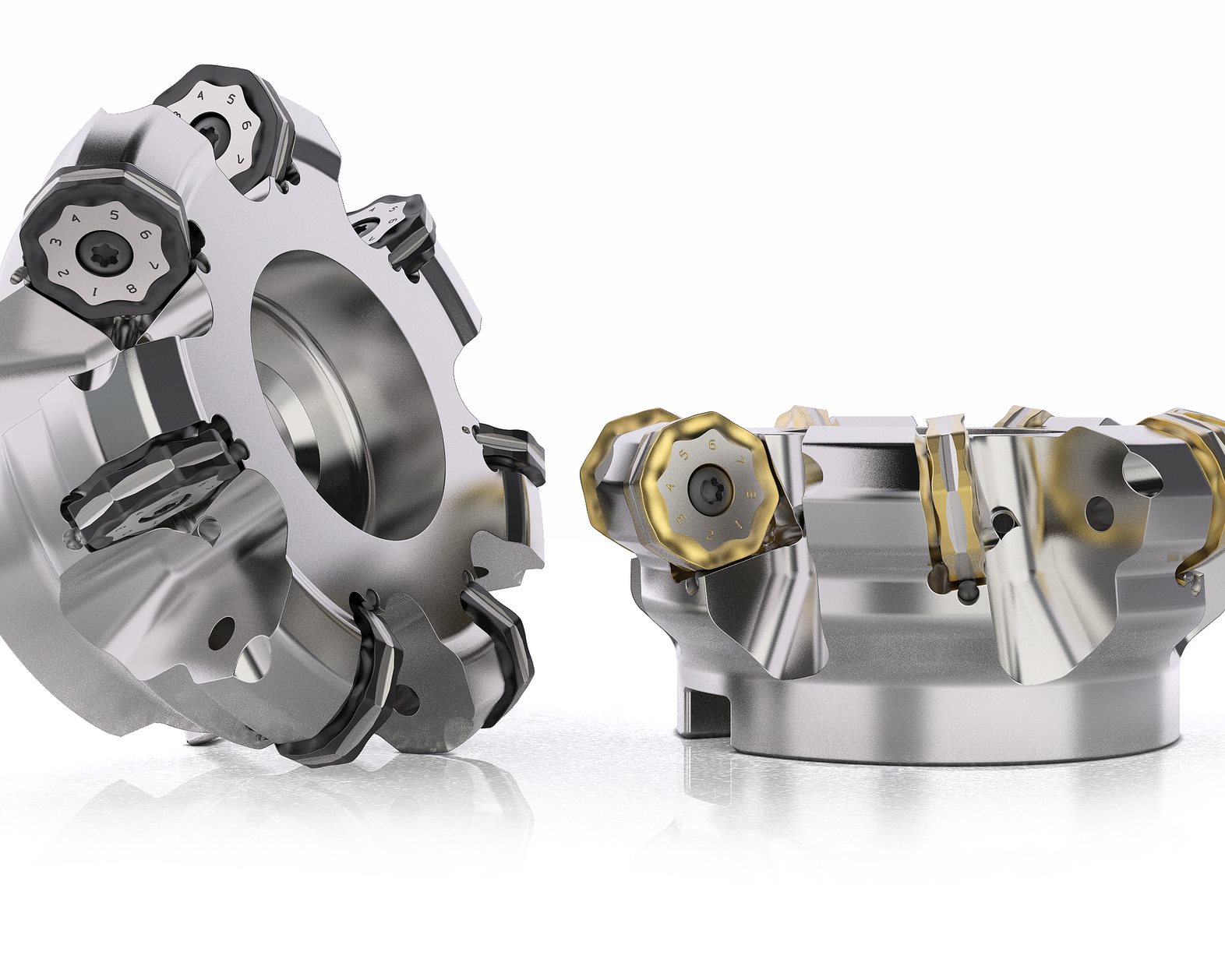
The High Feed Double Octomill is a high-performance face milling cutter designed for efficiency and cost-effectiveness.
This tool is ideal for face milling applications, offering a combination of high material removal rates and low cost per edge.
Key Benefits and features:
- Double-sided inserts: Each insert has 16 cutting edges, maximizing the tool's lifespan and reducing costs.
- High feed rates: The design allows for high feed rates, improving productivity.
Go to the products
Seco’s exchangeable head milling system is the smaller diameter range alternative to indexable milling cutters. They allow for quick and easy changes between various solid carbide milling head profiles, optimizing milling operations and reducing costs.
The X-Head end mills offer versatility with different shank lengths and long-reach capabilities and tool changes are simple, requiring only a wrench while the shank remains in the machine, eliminating the need to reset tool lengths with exchange accuracies within 50 microns.
Go to the products
Seco high feed end mills are the smaller diameter range alternative to exchangeable head milling systems. They feature an optimized front-end geometry allowing for higher feed rates, reduced vibrations and tool deflection.
These tools are ideal for deep and shallow workpiece features, 3D profiling in mold and die applications, and machining in unstable conditions, excelling particularly in plunge milling methods.
Go to the products
Inline Content - Sugar Form
Sugar Form url - https://info.secotools.com/acton/fs/blocks/showLandingPage/a/45194/p/p-00e5/t/page/fm/0
Frame height - 500 px