Gearing up for the win
The production of new spiral bevel gears made CORDM look for improved machine time and higher quality in order to secure a contract.Gears are a core part of any industrial machine, and those manufactured by CORDM in the city of Verdun in northeastern France are used to power motors required in a host of critical applications such as rail transportation, oil drilling, construction, mining and wind energy production. The company’s roots stretch back to when it was founded in Belgium in the early 19th century by René De Malzine, whose initials gave CORDM its original name, RDM. The factory was moved to Paris during the First World War and then to Verdun in the early 1960s to bring it closer to the iron- and coal-mining industries. In 1982, the company was renamed CORDM having been acquired by a worker cooperative.
Joriss Quennouelle, Head of R&D at CORDM, says: “In late 2012, we took delivery of a new Gleason-Heller machine to bring our equipment up to date with the latest technologies and give us full control over the complete cutting cycle for gear production. We partnered with one of the big French universities to perfect the cutting path and control the milling process, using cutting tools from another supplier for producing straight bevel gears, and were very happy with the results.”
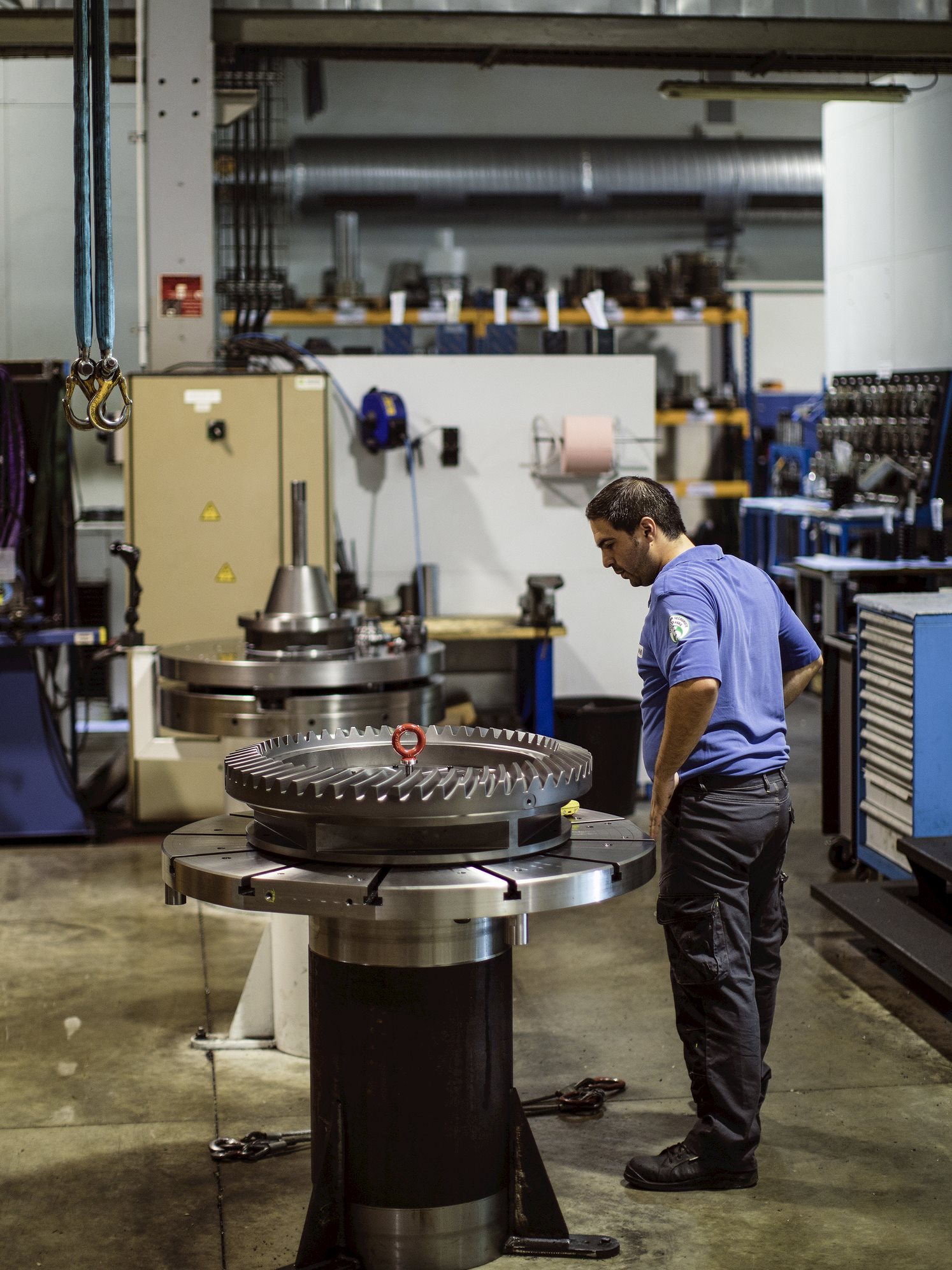
But when one of CORDM’s main clients, a mining and crusher equipment and services company, wanted to work with them on the production of a new range of machines requiring spiral bevel gears, it was very important for CORDM to secure the contract. “My coworker, design technician Nicolas Wiriot, worked on the gear design using Spiro software, and after a lot of research and hard work, we established that with the right machine tools, we could produce the gears required by the customer. We asked two tooling companies — including Seco — to bid for the project, and allocated a significant test budget to both. At the time, my priorities were quality and machine time. Once these were both satisfactory, we were able to look at the cost,” he says with a smile.
“Seco turned out to be much better in terms of both quality and speed and from then on, we have maintained a really solid partnership across multiple projects. We have a very good relationship with their Custom Tooling Development Engineer Eric Porte, and are constantly looking at improvements and new solutions we might introduce,” Quennouelle enthuses. “We worked with Seco prior to 2014, but this was a significant change for us.”
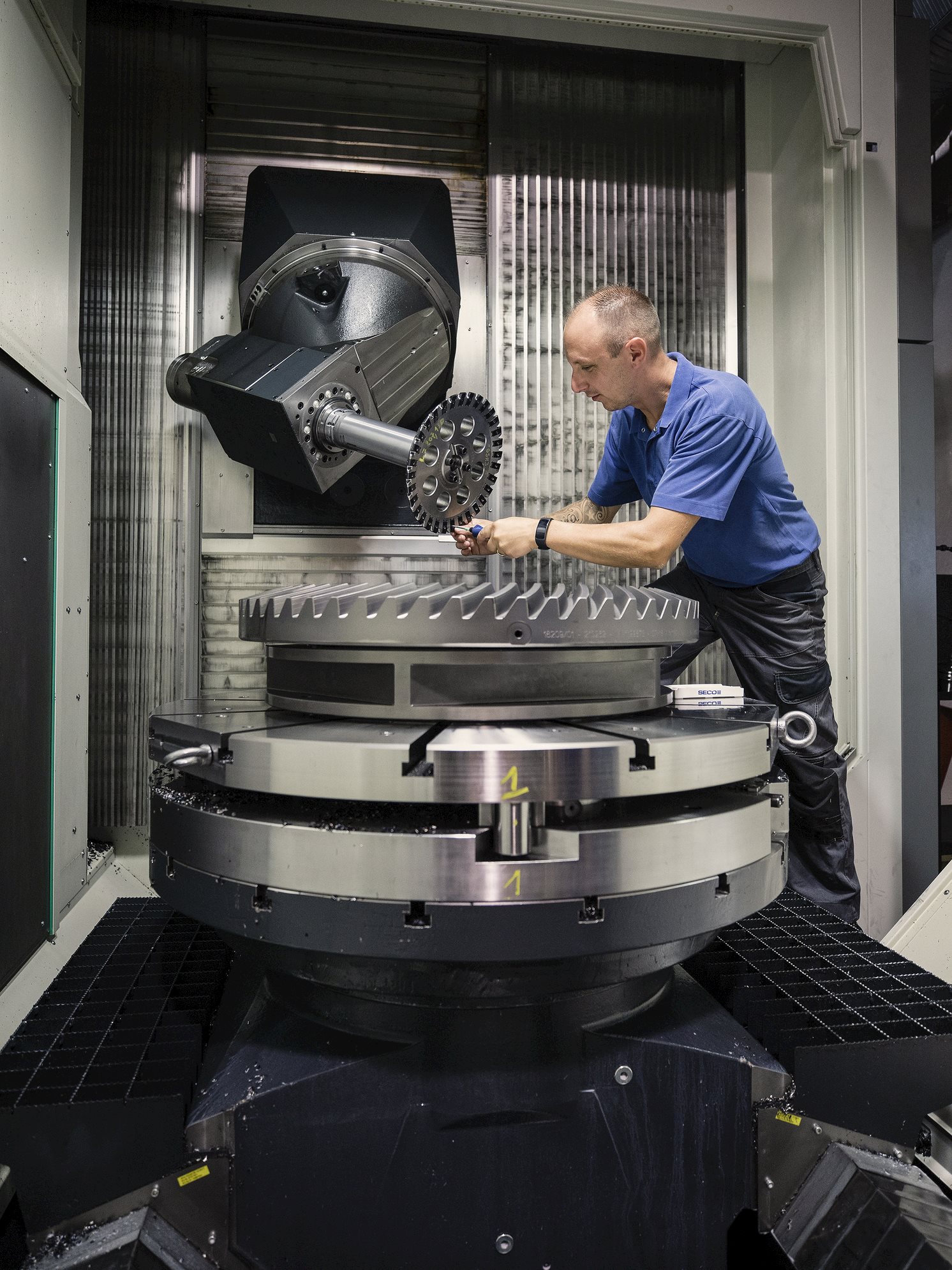
As with any large-scale project, there have been some teething problems. In this instance, CORDM were experiencing some issues with the cutting edge wearing away, but these were solved by modifying the geometry of the cutting insert. “We revalidated all the tool trajectories to ensure that no collisions would occur, and Seco produced a coupling which we tested before sending samples to the client,” he says. “Indeed, we’ve always had positive feedback from our customer since we began producing these spiral gears in mid-2017, and since the start of 2018, we have been turning out 90 drive gear-and-pinion sets every month.”
“We have many more projects that are in development or in the pipeline which will benefit from the strong relationship we’ve developed with Seco, and we’re very much looking forward to continuing this partnership into the future.”
FAST FACTS:
Problem: | | Solution: | | Result: | |
CORDM needed the right tools to produce high-tech spiral bevel gears | | Seco provided a 360° solution of hardware, software, and follow-up to allow CORDM to machine the gears they needed | | A high-performance and high-quality production line ensuring full customer satisfaction | |